TVET Master Perspective
The Malaysian semiconductor industry boasts impressive growth and global recognition. However, Deputy Minister of Investment, Trade and Industry Liew Chin Tong recently highlighted some crucial challenges hindering further advancement:
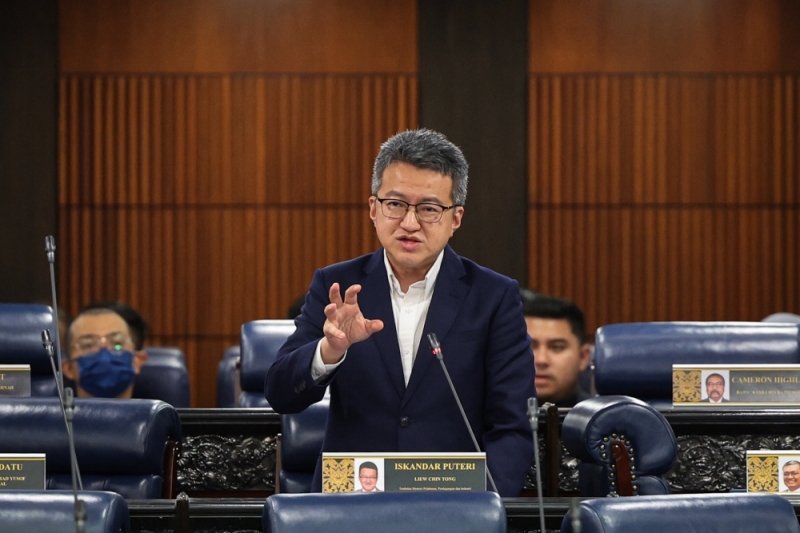
- Low-skilled labor dependence and automation resistance: Many companies, particularly SMEs, rely heavily on foreign workers and hesitate to embrace automation. This dependence limits productivity and technological leapfrogging.
- Domestic talent drain: Salary disparities with neighboring countries, like Singapore, entice skilled engineers and technicians to cross borders, weakening the local talent pool.
- Systemic underpaid workforce: The median manufacturing wage falls short of the national average, making STEM careers financially unattractive for young Malaysians. This discourages investment in STEM education and vocational training, exacerbating the talent shortage.
So, how does Malaysia go about balancing automation and talent challenges?
TVET Master Insight
Balancing automation and talent challenges in Malaysia’s semiconductor industry is not easy. Nevertheless, below are some key insights.
- Bridging the skills gap: Implementing robust TVET programs focused on automation, precision engineering, and advanced semiconductor processes can create a competent local workforce, reducing reliance on foreign workers.
- Enhancing industry-academia collaboration: Partnerships between TVET institutions and semiconductor companies can tailor training programs to meet industry needs and ensure graduates possess the relevant skills. Academy in Industry (Aii) could be the answer in addressing challenges in developing local talents.
- Promoting attractive STEM careers: Addressing the salary disparity is crucial. Government incentives, tax breaks, and scholarship programs for STEM students can increase the appeal of these careers.
- Strengthening TVET infrastructure: Upgrading equipment, facilities, and curriculum in TVET institutions is essential to ensure graduates are equipped with the latest technological knowledge and practical skills.
The Road Ahead:
Malaysia’s ambitious National Industrial Master Plan 2030 aims to double the median manufacturing wage, from the current RM2,205 per month (2022) to RM4,510 per month by the year 2030. a positive step towards attracting and retaining talent. By actively addressing the automation, talent drain, and wage challenges, the country can harness the full potential of its semiconductor industry and establish itself as a global leader in high-tech manufacturing.
Note: If your company is not in semiconductor industry but wants to explore on upskilling or reskilling your current or future employees, you may want to explore on National Dual Training System too.